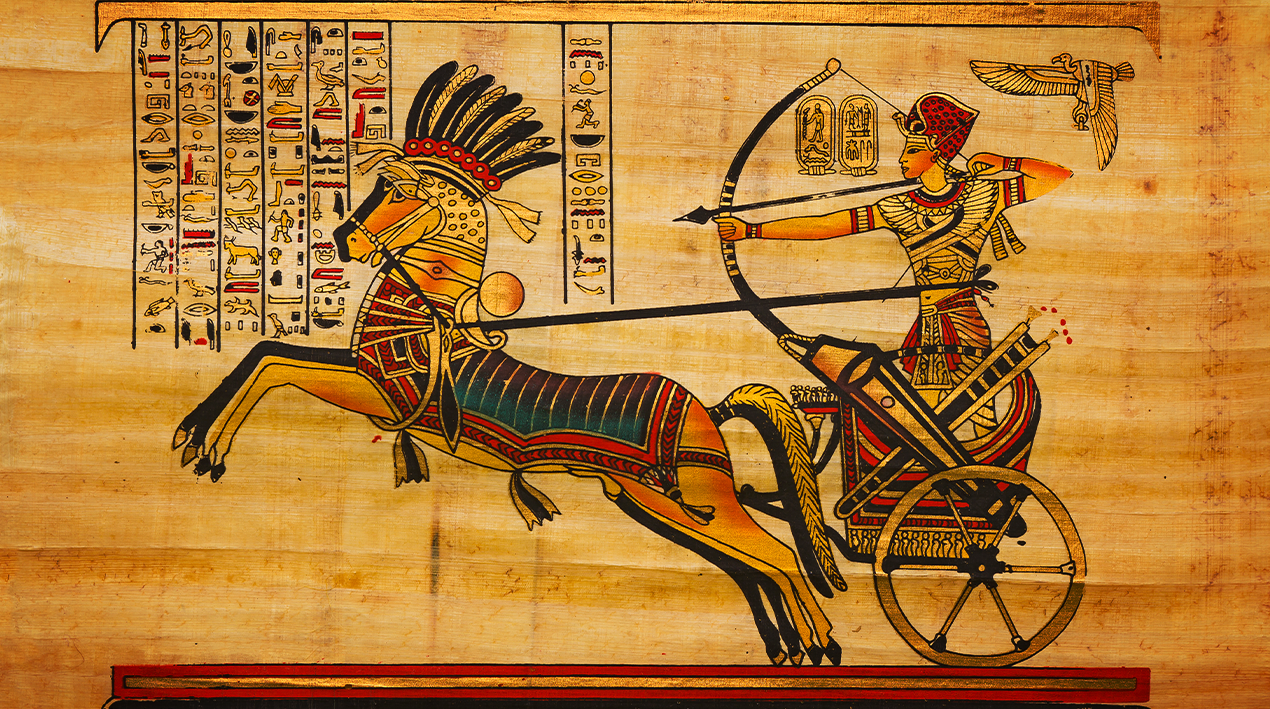
Neste primeiro post sobre óleos básicos, farei um relato de alguns dados históricos da evolução dos óleos minerais e das tecnologias desenvolvidas para a melhoria de sua qualidade.
A tecnologia dos óleos básicos passou por muitas etapas na sua evolução. Na primeira etapa, utilizava-se gorduras animais como lubrificantes. Inscrições antigas, datadas de 1650 A.C. (Antes de Cristo), mostram o uso de óleo de oliva para lubrificar as pranchas de madeira sobre as quais os egípcios transportavam seus monumentos e os eixos dos carros de guerra e de corrida do antigo Egito eram engraxados com sebo de carneiro. Nos tempos romanos, matérias-primas como a semente de colza, óleos de mamona e de palma eram usados como lubrificantes, o mesmo acontecendo com óleos de baleia. Pouca coisa mudou ao longo dos 3000 anos que se sucederam. Nas sociedades ocidentais, em 1852, os óleos minerais, derivados do petróleo, tornaram-se disponíveis pela primeira vez. Eles não foram amplamente aceitos no início, porque não tinham desempenho tão bom quanto muitos dos que eram derivados de origem animal. No entanto, a partir de 1880, quando se desenvolveu o primeiro processo de desparafinação do petróleo, os lubrificantes naturais foram sendo substituídos pelas graxas e óleos de petróleo, que eram muito mais baratos. O aumento da demanda por automóveis provocou uma crescente necessidade por óleos lubrificantes melhores. Rapidamente, os produtores de lubrificantes tiveram que desenvolver novos processos para disponibilizar produtos de melhor qualidade a partir do petróleo.
Por volta de 1930, surgiu o processo de beneficiamento a solventes como uma tecnologia viável para melhorar o desempenho/qualidade do óleo básico, usando solventes razoavelmente seguros e recicláveis. Ainda hoje, a maioria dos produtores de óleos básicos em todo o mundo usam este tipo de processo. Este processo de tratamento tem suas limitações e a sua eficiência quanto à eliminação de impurezas é de cerca de 60%. Ou seja, de 40 a 50% das impurezas que estão na estrutura química permanecem no óleo básico, cabendo aos aditivos melhorar a performance do lubrificante.
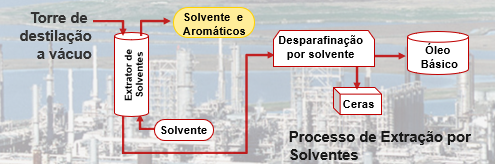
* Remove 50 a 60% das impurezas através da extração
* Remove as ceras por resfriamento
* Solventes usados em ambas as etapas
* Produz óleos básicos que são perfeitamente adequados a outras aplicações
As primeiras iniciativas para introdução de processos mais efetivos para a melhoria do grau de pureza dos óleos básicos minerais se deram nas décadas de 50 e 60. O primeiro desses processos, denominado de "hidrotratamento", envolve o uso de hidrogênio e tem como objetivo remover impurezas, estabilizar componentes mais reativos, melhorar a cor e aumentar a vida útil do óleo básico. Hidrotratar, por si só, geralmente, não é o suficiente para dar o nível de qualidade necessário para um óleo básico. Em adição, o "hidrocraqueamento" veio para complementar o processo. É uma forma mais severa de hidrotratamento. As moléculas do básico são reorganizadas e, algumas delas, quebradas para ficarem menores. Há um rearranjo molecular. Quase todo o enxofre e nitrogênio são removidos, e muitos compostos aromáticos são saturados pelo hidrogênio. Isso faz com que o óleo básico passe a ter uma maior resistência à oxidação (resistência à degradação = maior vida útil). Além disso, o índice de viscosidade se torna mais alto e o ponto de fluidez é rebaixado, tornando o óleo mais fluido a baixas temperaturas.
Como o processo com hidrogênio não consegue resolver satisfatoriamente a questão da formação de cera a baixas temperaturas, os produtores de lubrificantes continuaram pesquisando processos, com o objetivo de melhorar ainda mais a qualidade dos óleos básicos de origem mineral. Foi assim que as primeiras tecnologias de "Desceramento Catalítico" e "Hidroisomerização" foram introduzidas e começaram a ser comercializadas na década de 70.
A Chevron, em sua planta de Richmond, Califórnia, em 1984, foi a primeira empresa do segmento a combinar os processos de desceramento catalítico com hidrocraqueamento e hidroacabamento. Esta foi a primeira demonstração comercial de uma rota de hidroprocessamento (Catalytic Dewaxing and Wax Hydroisomerization) para fabricação de óleos básicos premium. Em 1993, a Chevron comercializou o primeiro processo de isomerização e desceramento moderno no mundo. Este processo foi desenvolvido por ela no final da década de 80.
O "Hidroacabamento" é a etapa final do processo de beneficiamento realizado nas modernas plantas de produção de óleos básicos minerais premium. São utilizados equipamentos sofisticados para dar uma espécie de polimento final para o óleo básico. Em essência, as poucas impurezas restantes são convertidas em moléculas estáveis.
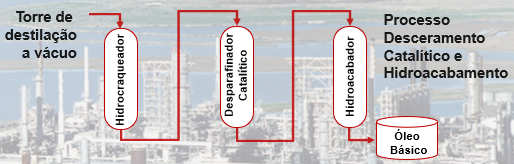
* Reorganiza as moléculas
* Converte as ceras em iso-parafinas de alta qualidade
* Converte 98 a 99.99% das impurezas em lubrificantes de alta qualidade
* Não utiliza solventes
* Permite fabricar os mesmos produtos a partir de diferentes fontes de petróleo
Os primeiros lubrificantes verdadeiramente sintéticos, derivados dos silicones e poliolefinas, foram desenvolvidos nos Estados Unidos no começo da década de 30. Porém, também existem relatos históricos de que, na mesma década, um alemão, Dr. Hermann Zorn, estava à procura de um lubrificante com propriedades semelhantes aos óleos derivados de petróleo, sem as indesejáveis deficiências, como alto ponto de fluidez, baixa resistência à oxidação a altas temperaturas, tendência a formação de borra e depósitos em motores a combustão etc. Mas foi no início da década de 40 que, na Alemanha, se intensificou o desenvolvimento dos lubrificantes sintéticos, uma vez que o acesso do país ao petróleo estava se tornando cada vez mais escasso. O primeiro teste no mundo real para esses lubrificantes ocorreu durante a Segunda Guerra Mundial, quando as forças alemãs e americanas começaram a usar óleo de base sintética em motores de aviões. Eles notaram que os sintéticos proporcionavam uma partida mais fácil do motor em climas mais frios (devido ao alto índice de viscosidade) e significativamente diminuíam os depósitos de borra que se acumulariam em radiadores de óleo ao usar lubrificantes convencionais (derivados do petróleo bruto). Os Estados Unidos relataram amplo trabalho com lubrificantes fluoretados em 1951.
O interesse atual pelos lubrificantes sintéticos obedece aos regulamentos ambientais promulgados por organismos internacionais, que exigem produtos mais amigáveis ao meio ambiente. Além disso, os fabricantes de veículos e equipamentos estão exigindo lubrificantes com vida útil mais longa, volatilidades mais baixas e maior eficiência energética. Em alguns casos, esses lubrificantes são obrigados a trabalhar em regimes de temperatura e pressão mais severos. No sentido estrito do termo, lubrificantes sintéticos são produtos químicos, embora alguns óleos vegetais e de plantas estejam incorretamente incluídos na categoria geral. Entretanto, a maioria é fabricada ou sintetizada em fábricas de produtos químicos pela reação dos componentes para fazer o produto final desejado. Exemplos disso incluem as poli-alfa-olefinas, diésters, ésteres de poliol e fluidos de silicone. Suas propriedades e grau de pureza variam de acordo com a família química. As características destes básicos permitem que eles sejam usados em uma ampla faixa de temperatura, mantendo excelente estabilidade à oxidação. Normalmente, o custo destes lubrificantes é mais elevado. Porém, devido a sua maior durabilidade e consequente maior disponibilidade do equipamento, em algumas situações, a relação custo-benefício é bastante favorável. Os fluidos de base sintética muitas vezes são materiais bem definidos. Resumindo, nos produtos finais para uso, eles podem oferecer:
* Utilidade em amplas faixas de temperatura
* Boa estabilidade
* Vida útil longa
* Características singulares de desempenho
Os lubrificantes sintéticos possuem qualidades desejáveis e indesejáveis. Daí a importância de se harmonizar o lubrificante correto com a aplicação pretendida. Por exemplo: para um compressor de parafuso, a melhor opção é um óleo sintético de base PAO (poli-alfa-olefina); já para um compressor de pistão, a melhor opção é um produto à base de diéster. O fato é que a grande variedade de lubrificantes sintéticos comercializada atesta que um tipo de lubrificantes sintético não funcionará para todas as aplicações.
Concluindo, para a maioria das aplicações, os óleos minerais derivados do petróleo continuam prestando desempenho satisfatório a baixo custo. Para aplicações mais rigorosas e extremas, onde se depara com baixíssimas ou altíssimas temperaturas, período de troca muito longos, por exemplo, existem lubrificantes minerais "não convencionais" (premium) à base de petróleo, ésteres vegetais e lubrificantes sintéticos. Todos os três são denominados, de maneira imprecisa, mas conveniente, de "sintéticos".
Bem, pessoal, creio que não ficou dúvidas a respeito do quanto se investiu em tecnologia de processo para chegarmos ao status atual, onde contamos com óleos básicos de altíssima qualidade. Tudo isso foi feito para disponibilizar aos consumidores lubrificantes de alta performance que possam atender plenamente as mais rigorosas condições de uso, nas mais diversas aplicações.
No próximo post, continuaremos falando sobre óleos básicos. Abordaremos detalhes sobre sistema de classificação do API (American Petroleum Institute) para a qualidade dos óleos básicos e, também, traremos gráficos de testes comparativos entre os óleos básicos minerais premium e sintéticos.
Não se esqueçam de deixar suas dúvidas e sugestões de temas no campo destinado a comentários. Até o próximo correio técnico!